- We are flexible and solution-oriented.
- We prepare your staff for working independently in this specific environment through targeted coaching and/or training.
- We develop solutions together with you. You benefit from the know-how transfer.
- We source our know-how from a broad network with connections to experts, even from rare disciplines, and with experience in the development of highly complex systems.
- We have excellent relations and experience in cooperation with EASA and German and Swiss national authorities.
- We are able to develop and implement safe, “acceptable” solutions even in a short time.
- We always approach an efficient solution that is in line with aviation regulations and other requirements (e.g. business).
Consulting
During our consulting we work out the best solution together with you, so that you can work with the new / improved system later. Our consulting management covers, among other things, the development and implementation of quality systems
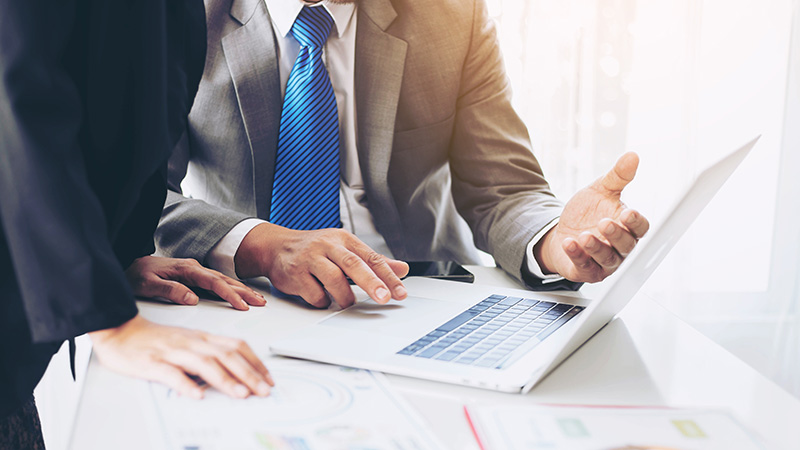
PART 21, SUBPART J (DOA)
The way to a certified (approved) aeronautical product (aircraft, engine, propeller) or to a modification of already certified (approved) products.
PART 21, SUBPART G (POA)
Safe processes / procedures produce safe products!
PART 145 (MOA)
Quality and safety require transparent and repetitive processes.
PART CAMO (CAMO)
PART-CAMO imposes organizational requirements on operations for management and continuing airworthiness.
EN 9100:2018
Quality and safety require transparent and repeatable processes.
SAFETY MANAGEMENT SYSTEM (SMS), ORGANISATION
The objective of safety management is to identify hazards to aviation safety and to mitigate or prevent the associated safety risks before they lead to accidents or incidents.
SUPPORT OF CERTIFICATION PROJECTS (TYPE APPROVALS)
Products (aircraft, engines, propellers), as well as parts installed in them, require certification in accordance with applicable regulations. The scope of certification is determined by the category of the aircraft.
ADVANCED PRODUCT QUALITY PLANING (APQP)
The goal of this approach is to ensure the comprehensive product planning or a change to the product and ultimately the control that all phases of the product realization are completed on time and quality as agreed.
DRONES / UAS / UAV
–
INTEGRATED MANAGEMENT SYSTEMS (IMS) IN AVIATION
Especially in quality management systems that must implement the aviation legislation, there is often a challenge to utilise synergy effects in documentation, interfaces to other quality management systems, supplier management, staff qualification, continuous surveillance monitoring, work and operation planning, etc.
WHAT MAKES US UNIQUE?
WHAT MAKES US UNIQUE?
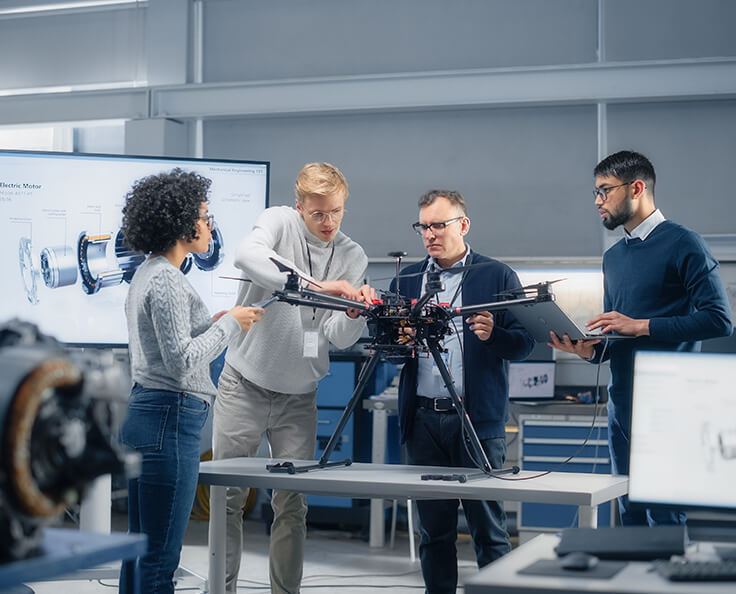